What Is The Extruder On A 3D Printer?
One of the critical components to understand is the extruder. In simple terms, the extruder is part of a 3D printer that controls the flow and deposition of filament material, like molten plastic or metal, onto the printing bed to create the desired object layer by layer.
The extruder consists of a motor and a series of gears, and it works in tandem with the hot end to heat, melt, and deposit the material during the printing process.
The table below highlights the differences between extruders on UV Resin and Epoxy Resin.
Types Of Extruders
The extruder pushes the filament to the hot end, where it is melted and deposited layer by layer to form the final object.
Bowden Extruder
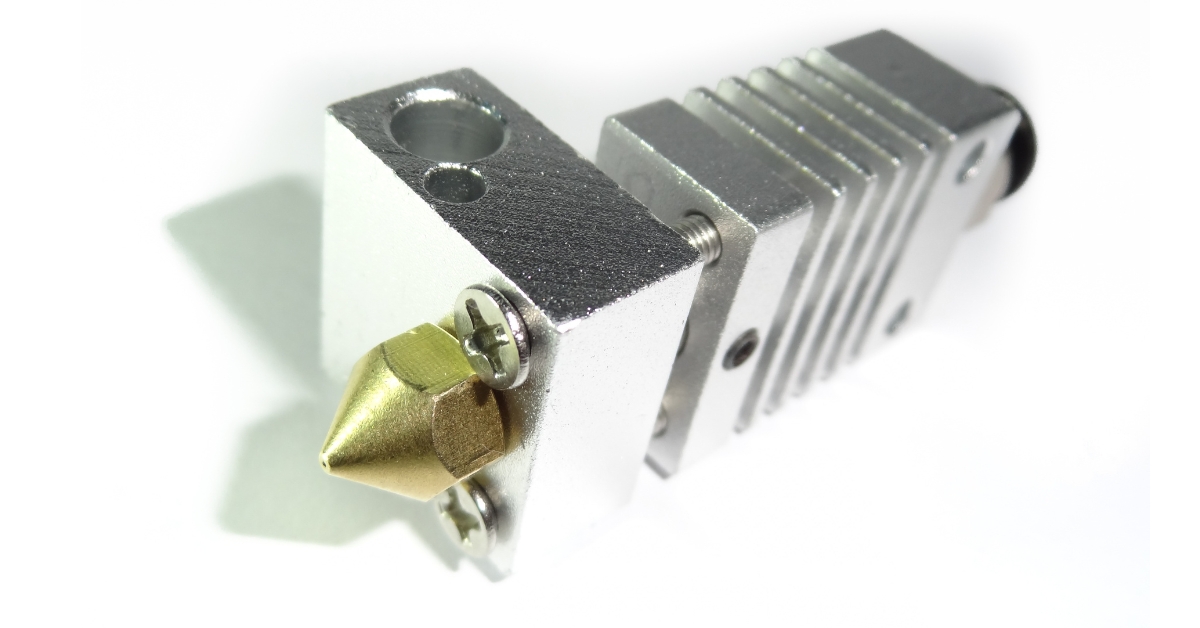
The Bowden extruder, one of the more popular options that can print faster, separates the cold end and the hot end by using a PTFE tube. The stepper motor responsible for pushing the filament is placed away from the 3D printer head, reducing the overall weight.
This design allows for:
- Faster printing speeds
- Less vibration and improved print quality
- Easier to maintain and clean
Direct Extruder
Direct extruders, unlike their Bowden counterparts, have the extruder motor directly attached to the hot end.
The proximity between the motor and nozzle minimizes the short distance a filament extruder has to travel, which can lead to:
- Better control over filament extrusion
- Higher compatibility with flexible materials
- Less potential for clogging
Geared Extruder
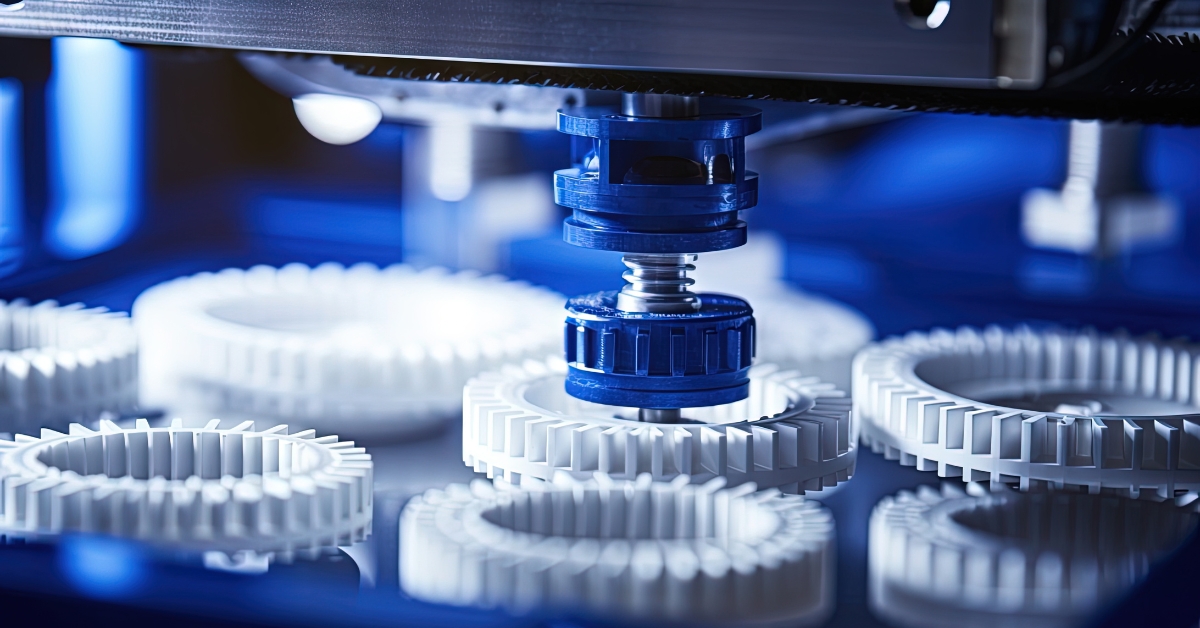
Geared extruders operate similarly to direct extruders but include a gear mechanism that increases torque from the stepper motor.
This enhancement has several advantages:
- Greater control over the discontinuous extrusion process
- Improved performance with various filament types
- Better handling of thicker successive layers
Parts Of An Extruder
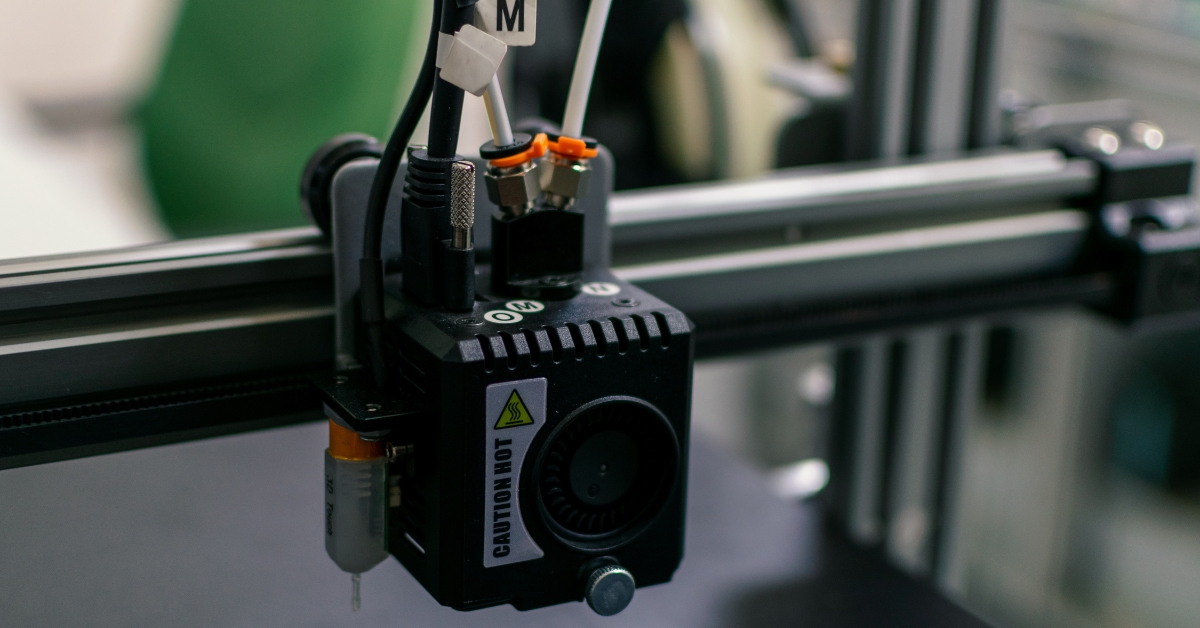
In binder jetting printers, the extruder plays a crucial role in the printing process. It controls the filament flow and pushes it through the nozzle to create the desired object. This video explains everything that you need to know, from how an extruder works to its parts.
Hot End

The hot end is responsible for melting the filament into a semi-liquid form, enabling it to be extruded through the nozzle. It consists of several parts, such as the heater block, thermistor, and heater cartridge.
The heater block houses the heater cartridge, which generates heat, and the thermistor, which monitors the temperature. Different materials require different nozzle temperatures, and the hot end must be able to accommodate these variations accurately.
Cold End
The cold end of the extruder is responsible for feeding and controlling the filament before it reaches the hot end.
It typically includes the extruder motor, gears, and a PTFE tube, which guides the filament to the hot end. This part ensures that the cold filament remains in its solid powder form until it reaches the hot end, where it melts and becomes extrudable.
Motor
The extruder motor is a key component in controlling the filament's print speed and flow. Usually, a NEMA17 stepper motor is used, which provides precise and consistent movement of the filament. In some cases, two extruders are employed, which use gears to increase the motor's torque and ensure better control over the filament flow.
Nozzle
Lastly, the nozzle is the part where the melted filament is extruded onto the building plate. Print nozzles are available in various sizes and melt materials, such as brass, stainless steel, and hardened steel.
The choice of nozzle material and size influences the print quality, speed, and the type of materials that can be used. For example, hardened steel nozzles are more durable and suitable for abrasive materials, whereas brass nozzles provide better heat conductivity and are ideal for printing with less-abrasive materials like PLA.
Understanding the function and importance of each part of an extruder body is essential for maintaining and troubleshooting your 3D printer. Ensuring that all components are functioning optimally will help you achieve the best possible print quality and prevent extruder-related problems that could affect your final object.
Materials and Filaments
When it comes to 3D printing, the type of powder material used plays a crucial role in the final outcome.
The PLA
As one of the most commonly used filament materials in 3D printing, PLA (Polylactic Acid) is a biodegradable thermoplastic derived from renewable resources such as corn starch and sugar cane.
PLA offers several advantages, such as:
- Easy to print with
- Low melting temperature (190-220°C)
- Produces minimal warping or shrinking
- Environmentally friendly
ABS
Acrylonitrile Butadiene Styrene (ABS) is a tough, impact-resistant thermoplastic often found in automotive and other consumer products.
With a higher melting temperature than PLA (220-250°C), ABS allows for sturdier prints suitable for functional parts. Some advantages of ABS include:
- Durable and strong
- Resistant to high temperatures
- It can be sanded and finished
Nylon
Nylon is a strong, flexible, and durable support material that has become increasingly popular for 3D printing. It's particularly useful for creating parts that require abrasion resistance or flexibility, such as gears and hinges. Some key features of Nylon include:
- High strength-to-weight ratio
- Ability to withstand high temperatures (up to 250°C)
- Resistant to chemicals
PETG
PETG (Polyethylene Terephthalate Glycol-Modified) is another popular filament in the 3D printing world due to its resilience, clarity, and ease of printing. It sits between PLA and ABS in terms of durability and temperature resistance, making it ideal for a wide range of applications. Its benefits include
- Low shrinkage and warping
- Good chemical resistance
- High transparency
Extrusion Process
The extrusion process of a 3D printer consists of three main sub-sections, which are integral to creating accurate and high-quality prints.
Preparation
Before the initiation of the printing process, the plastic filament must be fed into the 3D printer's extruder. The filament, which is stored on a spool, is guided through a tube to the extruder assembly.
Here, extruder motors push the printing filament through the extruder's gear system. The preparation phase ensures that the extruder is ready to deposit the filament onto the print bed, ultimately building the final object. It is essential to ensure that the filament is fed correctly and the extruder is appropriately calibrated to maintain the desired print quality.
Extrusion
The extrusion phase is where the actual 3D printing takes place. The filament is pushed through the nozzle by the extruder motor, which generates pressure, causing the filament to be heated, with its temperature and voltage being controlled to maintain the optimal extrusion process.
The hot end, which consists of a heater cartridge, a heat break, and the nozzle, is responsible for melting the filament and depositing it onto the print bed.
The extruder comes in two types: direct extruder and Bowden extruder. Direct dual extruders are directly attached to the print head, providing more precise plastic extrusion axis control, especially for flexible materials.
Bowden extruders are separate from the print head and use a PTFE tube to guide the filament to the nozzle. This design reduces the printing head's weight, allowing for faster printing speeds.
During extrusion, maintaining the correct temperature and pressure ensures that the filament flows smoothly and without interruption. Monitoring the nozzle temperature and adjusting it as needed can help avoid issues such as clogged nozzles, sticking filaments, or causing discontinuous extrusion.
Cooling
As the filament is extruded onto the print bed, it begins to cool, solidifying to form the final object. Proper cooling is vital to achieving a high-quality print. The cooling process involves using fans placed near the print head and a temperature-controlled print bed.
Ensuring adequate cooling helps maintain structural integrity, improving the overall quality of your 3D prints. It also helps avoid common issues such as warping, layer separation, or adding successive layers.
Balancing the cooling process with the extrusion process can enhance print quality and lead to a smoother, more consistent surface finish. In summary, understanding the Extrusion Process, which includes the Preparation, Extrusion, and Cooling sub-sections, can help you optimize your 3D printer's performance.
Proper calibration, temperature control, and cooling are crucial in achieving high-quality prints and making the most of your 3D printer's capabilities.
Understanding The Extruder Gearing
In the world of 3D printing, the extruder plays a vital role in producing accurate and high-quality prints. The extruder gearing, in particular, helps ensure that the filament is fed consistently and at the right pace to the dual extruder hot end.
Direct Drive
Direct Drive extruders are designed to be mounted directly on the stepper motor. The motor's torque drives the filament through the hot end, providing better control of the extrusion process.
As a result, direct drive extruders are favored for their increased precision and improved performance with flexible materials. However, they may have a slightly slower printing speed due to the added weight on the print head.
Hobbed Gear
A hobbed gear is a crucial component in both Bowden and Direct extruders. It is a gear with teeth that bite into the filament and drive it forward, ensuring a consistent flow of material.
The hobbed gear's design helps maintain a constant grip on the filament, reducing the risk of slippage and enhancing overall print quality.
Filament Drive Gear
The filament drive gear, also known as the extruder gear, is responsible for transmitting torque from the stepper motor (usually a NEMA17 stepper motor) to the filament.
The drive gear ensures consistent motion, allowing for precise material extrusion through the nozzle. The type and size of the drive gear can have a significant impact on print quality, as it directly affects the extrusion's accuracy and consistency.
Specific Extruder Models
In this section, we will discuss some popular extruder models for 3D inkjet printers, which include E3D V6, Micro Swiss MK10, Diabase Flexion, E3D Titan Aero, and LulzBot Mini. Each of these extruders has its unique features and advantages, making them suitable for various types of 3D printing projects.
E3D V6
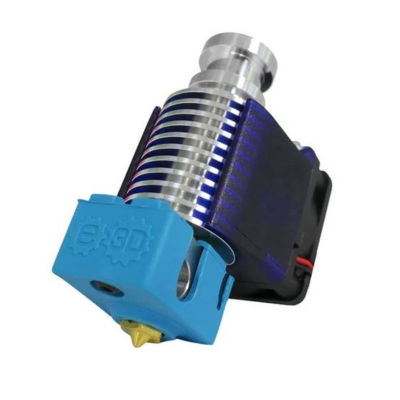
The E3D V6 is one of the most popular 3D printer extruders available. It is known for its high-performance capabilities and excellent print quality.
Some key features of the E3D V6 include:
- High-temperature performance, allowing for printing with a wide range of materials simultaneously
- Efficient heat sink design for optimal cooling and increased print speed
- Modular system, making it easy to upgrade and customize
The E3D V6 is compatible with a direct extruder and a Bowden extruder, providing flexibility for different binder setting FDM printer setups.
Micro Swiss MK10
The Micro Swiss MK10 is another great extruder option for FDM printers, specifically designed to work with the popular Wanhao and Makerbot models.
The MK10 boasts several features that improve the printing process, such as:
- All-metal construction, resulting in better heat distribution and durability
- Precise nozzle design for enhanced print quality
- Compatibility with various materials, including PLA, ABS, and flexible filaments
This extruder is an excellent choice for those seeking improved print quality and increased compatibility with a range of materials.
Diabase Flexion
For those working with flexible materials, the Diabase Flexion extruder is worth considering. This extruder is specifically designed to handle flexible filaments, such as TPU and TPE, with ease.
Some benefits of the Diabase Flexion include:
- Adjustable tension, ensuring proper grip on flexible filaments
- Compatibility with a wide range of 3D project printers
- Improved filament path, reducing the chances of filament jamming
The Diabase Flexion is ideal for those who frequently print with flexible materials and require a reliable extruder to handle these challenging filaments.
E3D Titan Aero
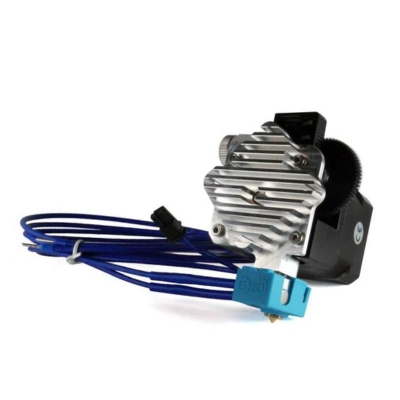
The E3D Titan Aero is an all-in-one extruder and hot-end system that combines the best features of the E3D V6 and the E3D Titan. This extruder offers an excellent balance of performance and reliability, making it a popular choice for many 3D printing enthusiasts.
Some key advantages of the E3D Titan Aero are
- Compact design, reducing the overall size and weight of the print head
- Integrated hot end and extruder, making it easier to install and maintain
- High-performance capabilities, supporting printing with various materials
The E3D Titan Aero is suitable for users looking for a compact, integrated extruder and hot-end system that offers excellent performance.
LulzBot Mini
The LulzBot Mini is a compact, user-friendly 3D printer that comes equipped with an extruder designed for reliable performance. Key features of the LulzBot Mini extruder include:
- Modular design, allowing for easy maintenance and upgrades
- Dependable performance for a wide range of materials, including PLA, ABS, and PETG
- Compatibility with various nozzle sizes, enabling users to customize print quality and speed